Real World Robotics Course
Real World Robotics is a hands-on project course to teach students about the complete robotic development process. The students develop their own dexterous robotic hand and control it using state-of-the-art machine learning techniques. The course was offered for the first time in the fall of 2023 and is offered yearly.
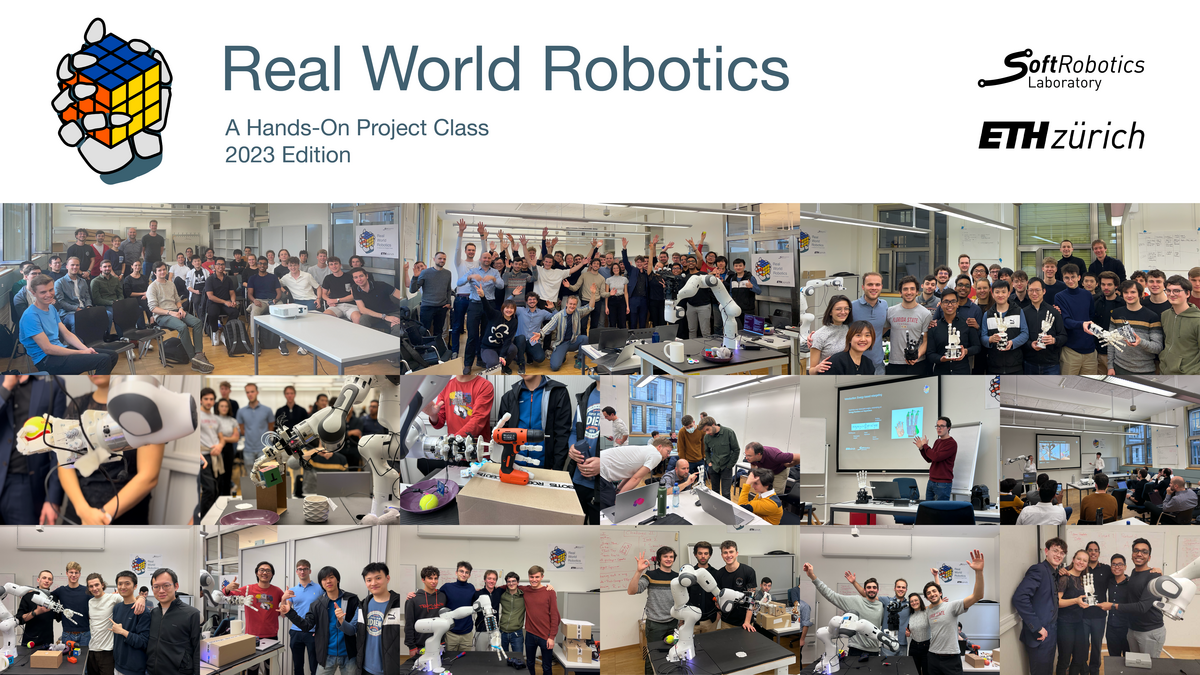
Course Abstract
This course guides RSC students through an entire robotic design process. Students will work in teams on a real-world robotics challenge: building an articulated robotic hand and programming a robust controller with reinforcement learning. The course covers high-level system design, robot simulation, fabrication, control, and testing. Students will learn the key theoretical concepts, develop hard- and software engineering skills, and gain practical engineering experience by building their own unique designs! Prerequisites assume introductive courses for robot dynamics and control. You will learn everything else on the way!
Lecturer: Prof. Robert Katzschmann
Occurence: Offered in the Autumn Semester at ETH Zurich.
Website: www.rwr.ethz.ch
The video tutorials are publicly available on our course website.
Objectives
Learning Objective 1: High-Level System Design
System and product design combined with requirement generation and verification are essential for this robotics project. The students will apply previously acquired system design knowledge and methods to a hands-on challenge.
Learning Objective 2: Robot Design and Simulation
Students will gain experience implementing and simulating robotic systems using modern design, modelling, and simulation techniques such as CAD and Isaac Gym. These techniques are essential in any design process to understand the expected system behaviour. This requires a thorough understanding of the system’s kinematics, dynamics, material, actuation principle, and physical limitations. Students will learn the theory and limitations behind modelling and simulation software.
Learning Objective 3: Robot Fabrication
Students will learn to use the previously designed CAD models for successful robot fabrication. Additionally, the iterative nature of the process will allow them to develop their critical thinking skills in assessing the limitations of their design as well as possible sources for improvements. Building the robot will equip students with essential skills for using robots in the real world.
Learning Objective 4: Control, Integration, and Testing
Students can directly apply the knowledge acquired in their baseline control courses. They will gain theoretical knowledge on how to model and develop intelligent control algorithms. Perception methods and alternative machine-learning techniques will be taught. They will gain experience in testing their robots’ performance in both hard- and software to enhance their design and suggest future improvements.
Learning Objective 5: Robot production
Students will learn how to choose between different prototyping methods to manufacture their robotic manipulators by understanding their respective limitations and requirements. They will also learn how to optimize the robot design to account for a specific manufacturing method.
Content
During this course, the students will be divided into teams and each group will independently develop an articulated robotic hand to solve a set of real-world robotic challenges, which will take place at the end of the course. The students will learn the key theoretical concepts required to model, manufacture, control and test their robotic manipulator, along with developing the programming, hardware and engineering skills through hands-on workshops.
This course is composed of tutorials, which will be available on the course website where the lecturer will provide all the necessary theoretical input, focus talks where robotic experts will present a particular aspect of the manipulator in detail, and workshops where the students will have the possibility to hands-on learn how to implement the solutions required to solve their challenge. Finally, there will be time slots to autonomously work on the manufacturing and development of the team's robot and an online forum will be available to help the students throughout the entire course.
This course is divided into 5 parts:
Part 1: Challenge introduction
- Identify the functional requirements necessary for the final challenge
- Evaluate the existing manipulator designs to optimize them for the specific task
Part 2: Robot Design
- Develop a CAD model based on the high-level system design.
- Integrate motors, tendons, molded components and other required materials in the design
Part 3: Robot Fabrication
- Come up with a fabrication method and plan using the presented fabrication skills.
- Fabricate the robot and its actuators based on the CAD model.
- Evaluate, modify, and enhance the fabrication approach.
Part 4: Robot Simulation
- Simulate the manipulator through a simulation framework
- Optimize the simulation parameters to reflect the experimental setup
Part 5: Control, Integration, and Testing
- Formulate the dynamic skills needed for real-life application.
- Develop traditional and learning-based control algorithms and test them in simulation.
- Integrate controller design into the fabricated robot.
- Build, test, fail, and repeat until the robotic manipulator works as desired in simple tasks.
- Upgrade and validate the robot for performance in real-world conditions and verify requirements.
Part 6: Product development
- Propose a manufacturing process to bring the robot from a prototype to the final product
- Optimize the robot for production
Literature
1) Toshimitsu, Y., Forrai, B., Cangan, B. G., Steger, U., Knecht, M., Weirich, S., & Katzschmann, R. K. (2023, December). Getting the Ball Rolling: Learning a Dexterous Policy for a Biomimetic Tendon-Driven Hand with Rolling Contact Joints. In 2023 IEEE-RAS 22nd International Conference on Humanoid Robots (Humanoids) (pp. 1-7). IEEE.
2) Liconti, D., Toshimitsu, Y., & Katzschmann, R. (2024). Leveraging Pretrained Latent Representations for Few-Shot Imitation Learning on a Dexterous Robotic Hand. arXiv preprint arXiv:2404.16483.
3) Egli, J., Forrai, B., Buchner, T., Su, J., Chen, X., & Katzschmann, R. K. (2024). Sensorized Soft Skin for Dexterous Robotic Hands. arXiv preprint arXiv:2404.19448.
4) Yasa, O., Toshimitsu, Y., Michelis, M. Y., Jones, L. S., Filippi, M., Buchner, T., & Katzschmann, R. K. (2023). An overview of soft robotics. Annual Review of Control, Robotics, and Autonomous Systems, 6, 1-29.
Prerequisites / Notice
Students are expected to have attended introductory courses in Robot Dynamics, Control Systems and Robotics.
The course size is limited to 36 students. For this reason, it is required to apply through a google form that is listed on the VVZ.
Course Information
Website: rwr.ethz.ch