Bridging the Gap: New Approach Enhances Simulation Accuracy for Soft Robots
Researchers at ETH Zurich’s Soft Robotics Lab have developed a novel data-driven framework to improve the accuracy of soft robot simulations. This innovative approach significantly reduces the sim-to-real gap, enabling more efficient and precise robotic systems with a wide range of applications, from automation to soft robotics.
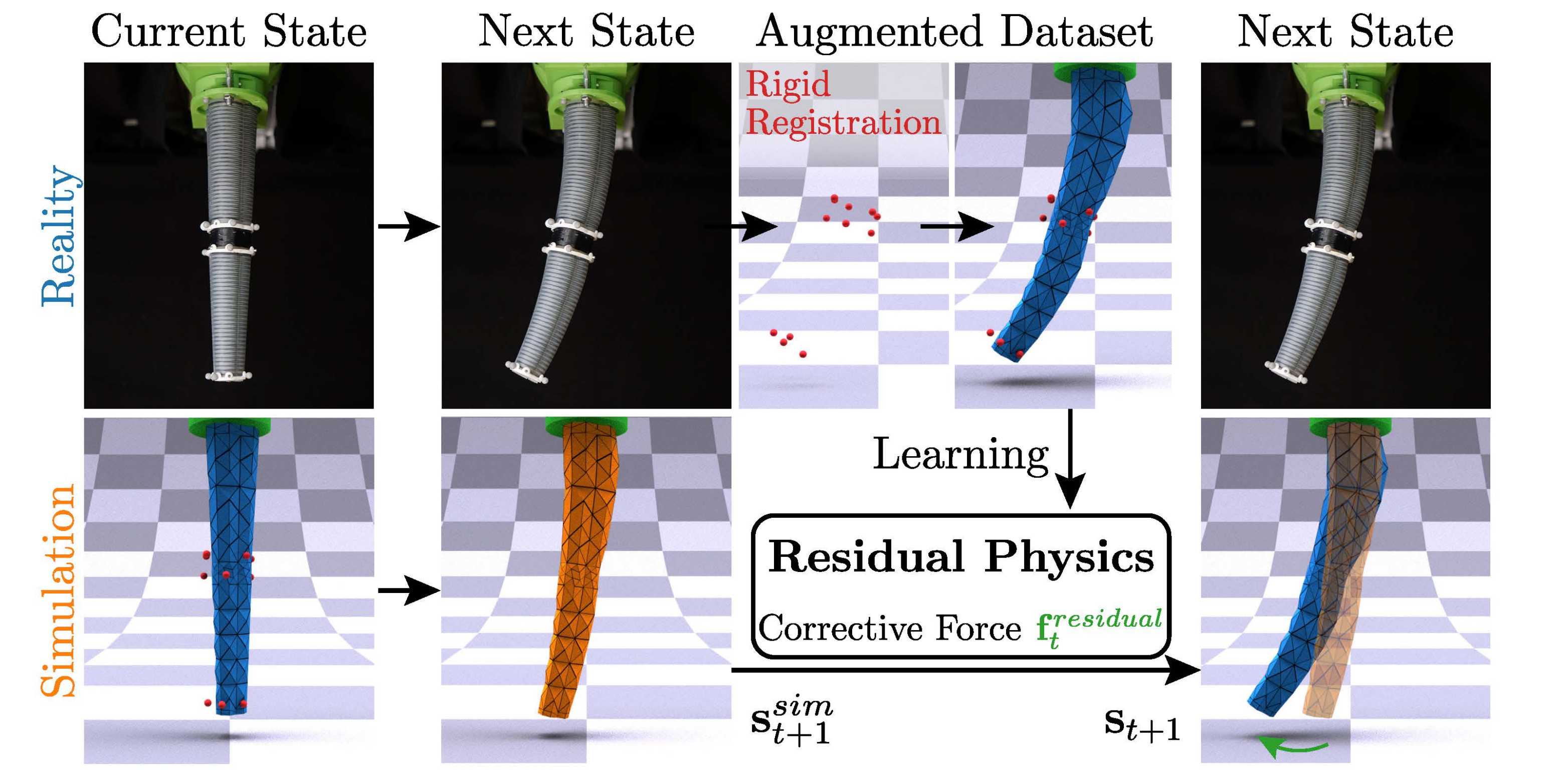
Accurately simulating the behavior of soft robots remains a key challenge in robotics due to the complexity of their structures and materials. To address this issue, researchers at ETH Zurich's Soft Robotics Lab, in collaboration with Harvard University and supported by the ETH AI Center, have developed a new framework that combines simulation with learned residual physics. The research, published in IEEE Robotics and Automation Letters, introduces a method that leverages real-world data to enhance the accuracy of existing soft robot simulators, closing the "sim-to-real" gap that often hinders real-world applications.
The Sim-to-Real Problem
Soft robots, made of flexible materials, are highly valued for their ability to perform complex tasks such as manipulation and interaction with delicate objects. However, accurately modeling their physical behavior in simulations is extremely difficult, as traditional simulators often struggle to replicate the effects of material properties like viscoelasticity, plasticity, and hysteresis. This discrepancy between simulation and reality, known as the "sim-to-real gap," complicates the process of designing and controlling soft robots for real-world tasks.
Innovative Solution: Learned Residual Physics
In this study, the researchers propose a residual physics framework that learns from real-world data to correct the errors in traditional simulation models. By using a combination of differentiable Finite Element Method (FEM) simulators and deep neural networks, the framework learns the residual forces that account for the modeling discrepancies, improving the simulation’s accuracy by up to 60% over traditional methods.
The framework is applied to two experimental setups:
- A silicone elastomeric beam
- A soft pneumatic robotic arm with complex anisotropic fiber reinforcements
By collecting data from these systems using sparse motion markers, the researchers trained neural networks to bridge the gap between simulated predictions and real-world observations. This hybrid approach significantly enhances simulation performance without the need for exhaustive system identification or the manual tweaking of physical parameters.
Key Results and Applications
The proposed method demonstrated superior performance compared to traditional system identification techniques, not only in accuracy but also in the robustness of the results. The implications of this work are far-reaching, offering improvements in:
- Soft robotic design: Enabling more accurate virtual testing before physical production
- Control optimization: Helping refine controllers for soft robots to ensure smoother and more precise movement
- Real-time simulation: Reducing computational costs while improving simulation fidelity
This breakthrough has the potential to accelerate the development of soft robotic systems used in fields such as healthcare, automation, and biomimicry, where the interaction between robots and the real world is highly dynamic and sensitive to changes in physical properties.
Collaborations and Support
The research was led by Robert Katzschmann, in collaboration with the first authors Junpeng Gao and Mike Y. Michelis, and the supporting author Andrew Spielberg. The project was supported by Credit Suisse, the ETH AI Center, and an Amazon Research Award, highlighting the interdisciplinary nature of the research, which brings together advances in machine learning, simulation, and robotics.
For further details, the full paper titled "Sim-to-Real of Soft Robots With Learned Residual Physics" is available in the external page IEEE Robotics and Automation Letters.