Vision Controlled Jetting for Robots
Fully functional systems and robots printed contact-free in a single process
Until now, complex assembly processes were necessary to produce functional systems made from different materials. We investigated high-resolution, large-build volume 3D printing methods. 3D inkjet deposition builds systems layer-by-layer. When a layer is flat, it is cured using polymerization induced by exposure to UV light. Previous methods used for example mechanical rollers to ensure each printed layer is flat before curing. The necessity for mechanical contact restricts the classes of materials available for printing. Additionally, we use wax with a low melting point as a support material that coats all structures. The wax support structure melts at 60°C, allowing us to print complex systems with cavities in a single pass.
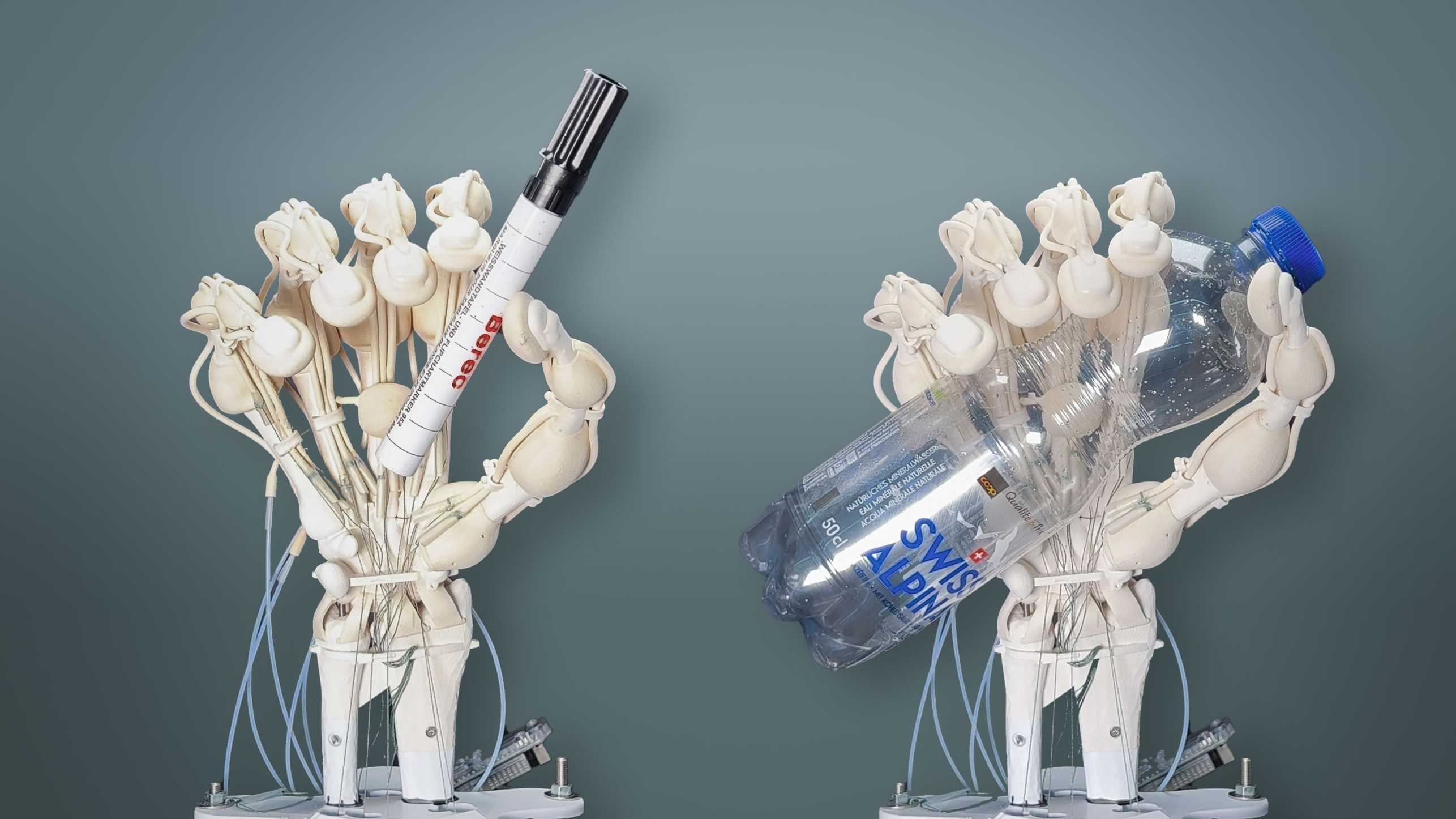
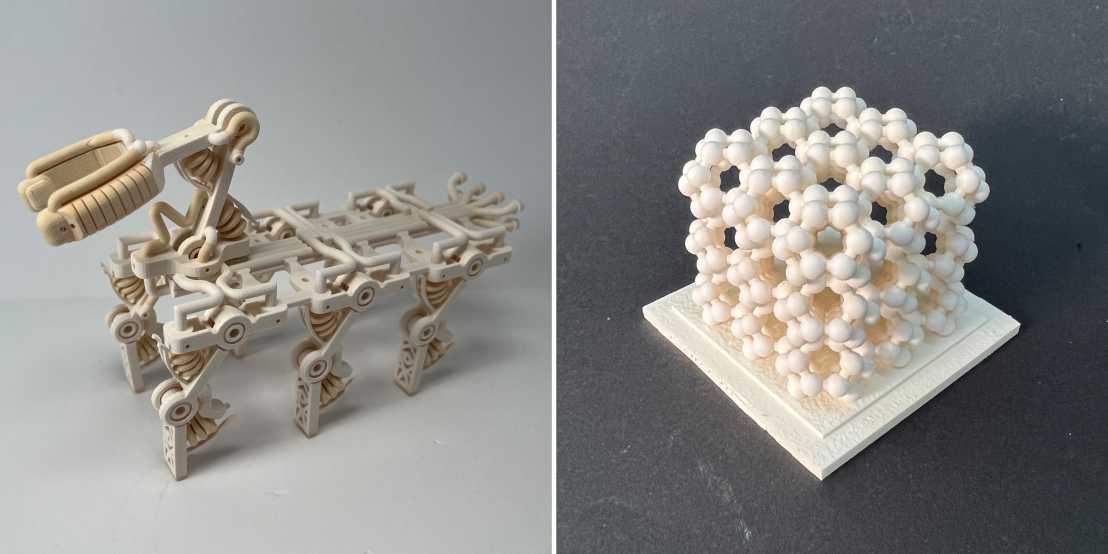
With our collaborators from Inkbit, we created a printing method called "Vision Controlled Jetting" that works contactless. It scans each printed layer and automatically compensates for unevenness by adjusting the subsequent layer. We can, therefore, print slow-curing polymers for the first time. These polymers create structures that are now, for the first time, low in viscosity and are resistant to UV light and moisture.
The use of our method requires no assembly for printed systems; the print was connected to motors and was immediately fully functional. The method easily extends to other robotic systems that can now be produced in a single pass and immediately fulfill their tasks. We demonstrated this on a biomimetic hand, a walking robot, an artificial heart, and complex metamaterials. This new technology enables countless applications, e.g., robotics and medical technology.
The work was featured in an ETH Zurich news article titled "Printed robots with bones, ligaments, and tendons".
external page Video (Credit: ETH Zurich / Nicole Davidson)